Compression Seal Fittings
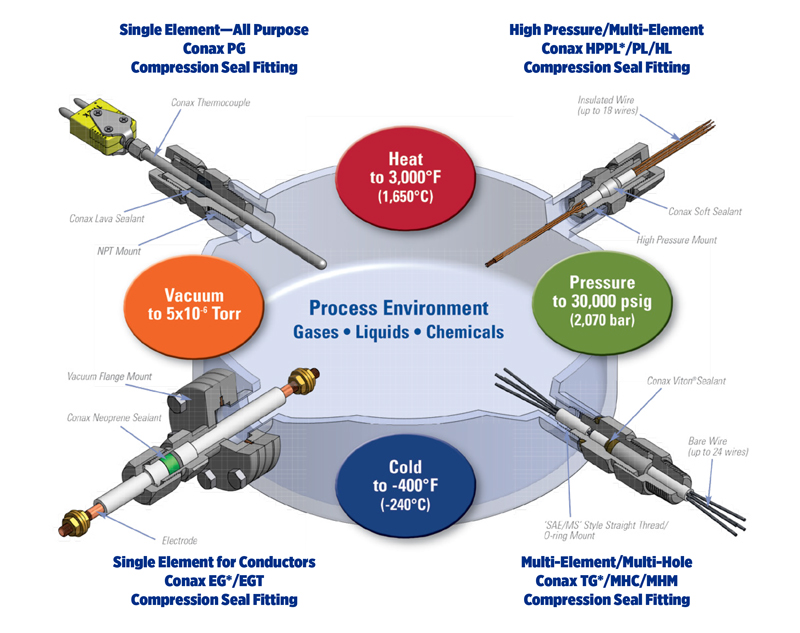
Innovative Conax solutions
Single element sealing
These compression seal fittings are used for sealing on a single element, such as a temperature probe, wire, electrode, tubewell, pipe, etc. These fittings are capable of sealing on items made of metal, glass, ceramic or plastic.
- Seal fitting (PG/HPG) series for sealing on anything from fragile tubes and soft cables to solid probes or instruments; element diameters range from 0.040″ (1.0 mm) to 1.50″ (47.5 mm) pipe.
- Midlock (MK) series for sealing on metal elements and/or in high vibration environments; stainless steel throughout—single ferrule is self-aligning.
- Electrode (EG) series power compression seal feedthroughs are fully isolating for electrical power or instrument isolation to 2000VDC; high pressure, high temperature and current capabilities.
- Electrode PTFE (EGT/HEGPK) series is fully isolating for bare electrical power leads or instrumentation isolation to 8000VDC; PTFE insulation and sealant material for high performance and chemical resistance.
- Split (PGS) series fittings seal cables and leads when larger probes or connectors are attached.
Multiple element sealing
These compression seal fittings are used when you need to seal multiple thermocouple, RTD or thermistor probes, tube bundles and liquid level sensors, or a variety of devices within a single fitting. The soft sealant technology seals against gases or liquids and resists element movement under pressure. Immersion lengths can be easily adjusted in the field. Individual elements can be set at different lengths to facilitate monitoring of multiple points.
- Transducer (TG) series for bare wire sealing where elements remain fully electrically isolated throughout the fitting; seals up to 16 solid wire conductors in wires sizes from 8–24 AWG.
- Multi-hole ceramic (MHC) series are non-isolating fittings for multiple elements up to .125″ (3.0 mm) diameter; seals 1–16 elements with adjustable immersion length for each element.
- Multi-hole metal (MHM) series has a flexible design for special hole patterns, irregular shapes and mixtures of element sizes; seals 1–27 elements with adjustable immersion length for each element.
- The split seal (SPGA/DSPGA) series for sealing elements that can pass through the fitting body but not the internal components; fittings carry both hydraulic and pneumatic catalog pressure ratings.
- Bearing sensor wire seal (BSWS/TWS) series are designed specifically for sealing on sensor leads in low temperature and pressure apps; ideal for embedded bearing temperature sensors, vibration sensors and proximity probes.
Multiple element sealing with factory installed lead wires
These compression seal fittings are used when multiple wire feedthroughs are required to carry power or instrumentation signals into pressure or vacuum environments. These fittings are manufactured with factory installed lead wires.
- High density (HD) feedthrough series utilize a compact and reliable wire sealing design—does not use epoxy or potting; seals from 12–60 wires per unit, 24 AWG, PTFE insulated.
- Power Lead (PL) series for high performance sealing from 1–18 larger gauge wires sizes 8–20 AWG; rated 600VAC/850VDC @ 55A max—available with or without conductors.
- Transducer seal fitting PTFE (TG24T) series utilizes 24 AWG PTFE insulated copper or thermocouple leads rated at 100VDC; seals up to 24 PTFE insulated, 24 AWG instrument leads per fitting to 8,000 PSig (551 bar).
- Transducer seal fitting fiberglass (TGF/TGM) series utilizes fiberglass insulated thermocouple wire for applications > 450°F (232°C); seals up to 24 high temperature insulated 20/24 AWG wires per fitting.
- High pressure (HPPL/HPEG) series for sealing on power leads or instrument leads in high pressure environments; for applications with pressures to 30,000 PSig (2,070 bar).
Application specific assemblies and custom configurations
-
These products have been custom designed for special use applications. Our team has the expertise and innovative ideas to create a customized solution for your most challenging applications.
- Hazardous location (HL) series fittings and feedthroughs are CSA certified.
- Hazardous location power lead (HLPL) series feedthroughs are ATEX & IECEx certified.
- Combo fitting (CB) series feature custom combinations of two fittings in one assembly.
- Fiber optic (FSA/FCA) feedthrough series; FSA is for sealing fiber optic cable inside a stainless steel sheath and without using epoxy, and FCA is a fiber optic cable assembly.
- Sample Probe Assemblies (SPA) and Retractable Sensor Assemblies (RSA) allow insertion/retraction of a sample tube or sensor under pressure via a process isolation valve. If you need engineering help to ensure you’re choosing the proper SPA for a specific application, we’ve created the Wake Frequency Solution Builder™ to generate immediate, online wake frequency calculations.
- Custom configurations can be created by Conax Technologies’ experienced engineers to fit your application. Examples include multi-hole seal fittings using holes of different sizes or non-standard hole patterns, sealants with non-concentric shapes, or custom mounting styles.
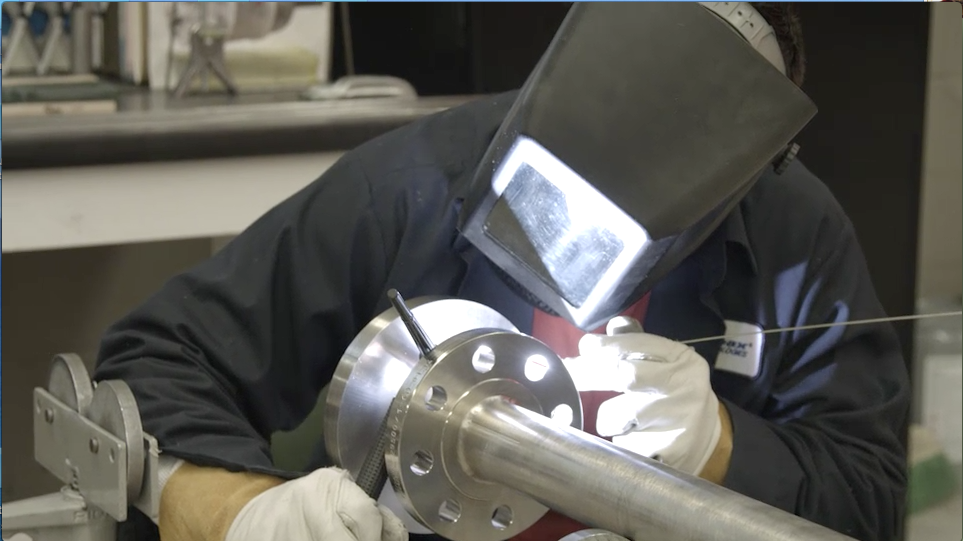